LG SMART PARK NAMED ‘LIGHTHOUSE FACTORY’ FOR FUTURISTIC MANUFACTURING TECHNOLOGY
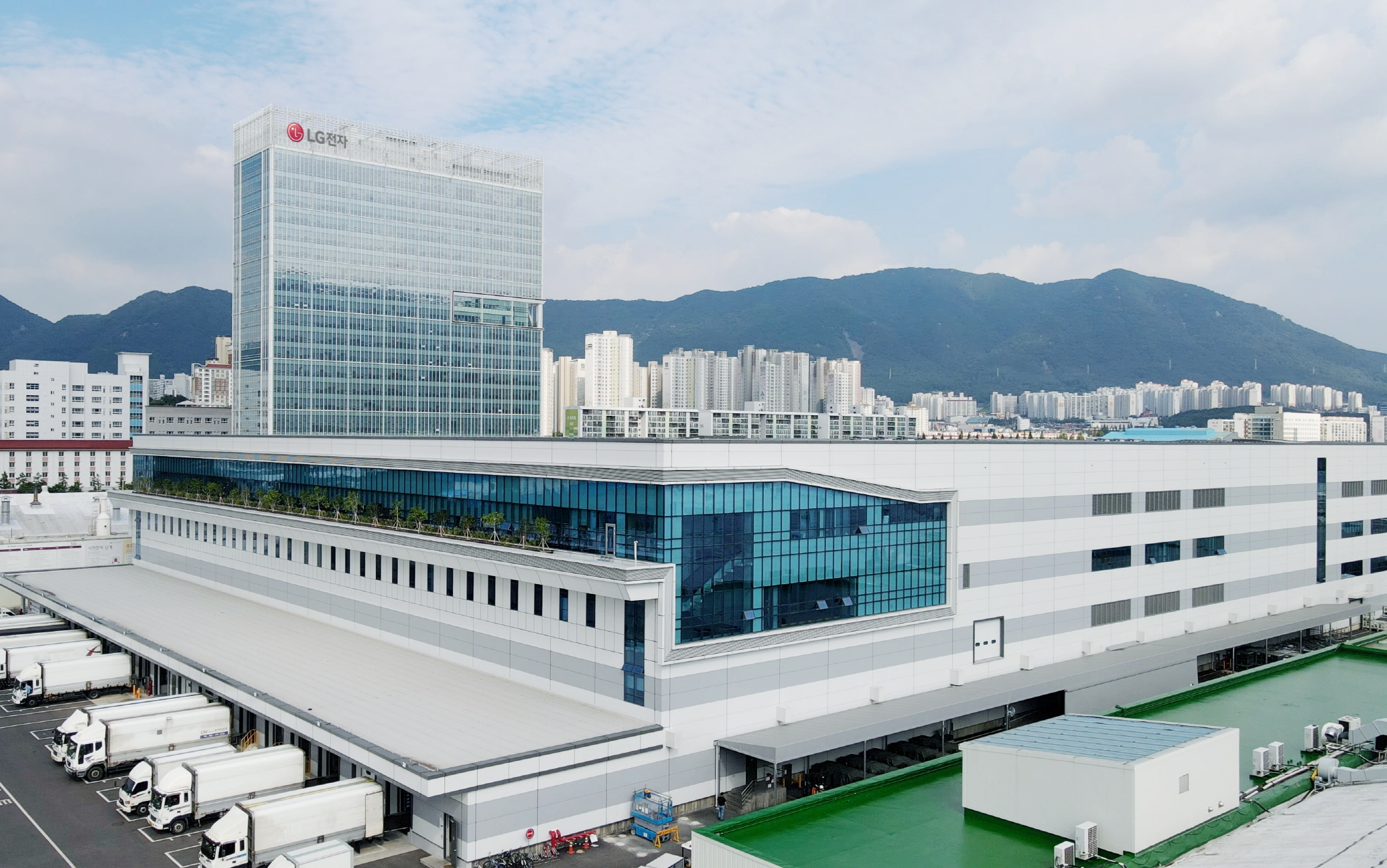
Jeddah, gulftech — LG Smart Park, a production base of LG Electronics (LG), has been selected as a Lighthouse Factory by the World Economic Forum (WEF).
Shaping the future of manufacturing, WEF “Lighthouse” facilities implement Fourth Industrial Revolution technologies, such as the Internet of Things, big data, artificial intelligence and robots, into manufacturing and supply chain operations to deliver a wide range of benefits, from increased production efficiency to enhanced environmental sustainability.
“As the world grapples with many challenges, it is remarkable to see how Lighthouses are yielding sustainability benefits while achieving business goals, which we call eco-efficiency.” said Francisco Betti, Head of Shaping the Future of Advanced Manufacturing and Value Chains, World Economic Forum. We need them to continue illuminating the way forward for the global manufacturing community by shaping a responsible future of manufacturing that works for people, society and the environment”
Over the past five years, LG has transformed its factory complex in Changwon, South Korea into LG Smart Park, a futuristic hub of home appliance manufacturing. The key elements of the transformation are a digitally-enabled end-to-end three-dimensional logistics system, an advanced analytics system based on edge computing technology and machine learning that predicts defects, and state-of-the-art facilities that can mass-produce multiple models to respond flexibly to customer requirements.
The newly implemented ‘digital twin’ technology enables the operation system to analyze production processes in virtual reality. It can predict if any issues will occur within the next 10 minutes and provide exact parts and materials for the assembling of each appliance with an accurate, up-to-the-minute status of the facility’s logistics operations. Sensors utilizing deep learning technology are installed throughout the factory to monitor each phase of production in real-time, helping factory workers to preemptively identify and resolve any possible issues. As a result, the defective return cost has been decreased by 70 percent, comparing the year from 2020 to 2021 while overall quality competitiveness1 and production efficiency2 have both been significantly strengthened.
Floors one, two and three at LG Smart Park employ an overhead conveyor system that quickly transports boxes containing refrigerator parts to the required production lines. Attached to each line as an intelligent warehouse that monitors inventory in real-time, enabling automated materials management, including the request of additional parts and supplies.
On the ground, automated guided vehicles (AGVs) leveraging stable 5G network connectivity transport parts and materials to wherever they are needed on site. Through its three-dimensional logistics automation system, the company can minimize the amount of warehouse space needed by 30 percent compared to conventional logistics systems, and shorten the time required for hourly materials transportation by 25 percent.1
LG Smart Park has also adopted the use of robots featuring an AI engine and camera to make the home appliance production process faster and safer. The robots undertake dangerous and complicated tasks, such as welding and the lifting of heavy parts and equipment.
LG plans to apply the innovative, smart production technologies pioneered at LG Smart Park to a total of 26 LG production facilities in 13 countries, accelerating the digital transformation of its global manufacturing network by 2025.
“LG Smart Park illustrates our strong commitment to adopting the revolutionary technologies as the leader of global premium home appliance market,” said Lyu Jae-cheol, president of the LG Electronics Home Appliance & Air Solution Company. “We are presenting a blueprint for the future of manufacturing, one that delivers better outcomes across environmental, economic and employment aspects.”